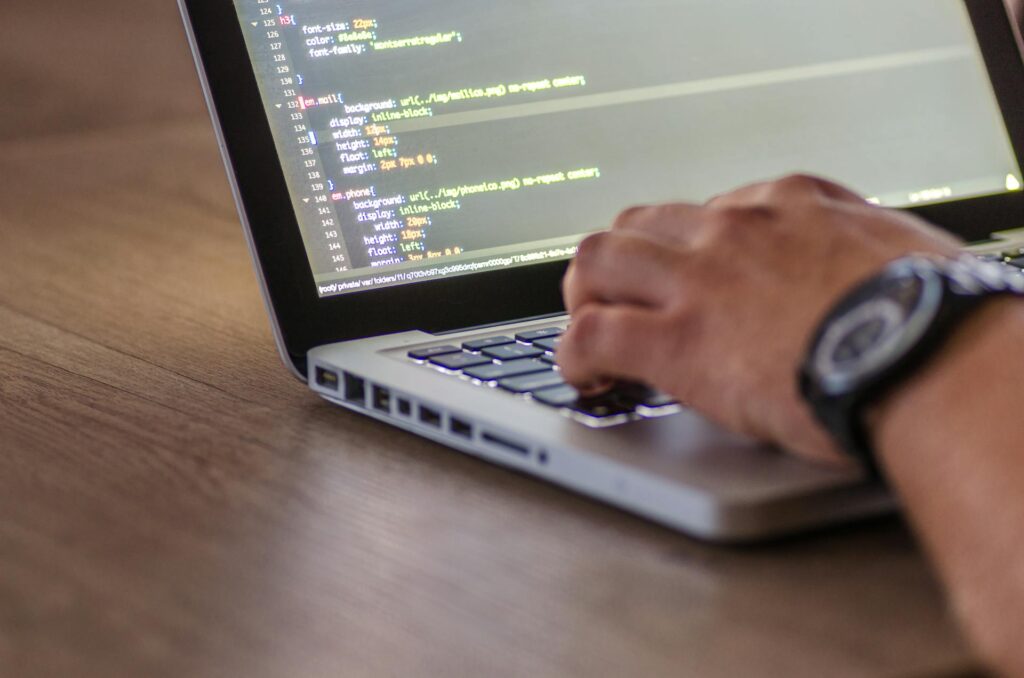
Product defects are a major challenge for businesses across industries. Whether in manufacturing, electronics, or consumer goods, defects lead to increased costs, dissatisfied customers, and damage to brand reputation. Even with stringent quality control processes, many companies still struggle with defects that slip through production. These issues not only impact profitability but also cause supply chain disruptions and regulatory compliance challenges.
Common Reasons Businesses Struggle with Product Defects
1. Inconsistent Manufacturing Processes
Manufacturing involves multiple steps, from raw material processing to final assembly. If these processes lack standardization, defects become inevitable. Variations in equipment settings, operator skill levels, and material quality can lead to inconsistencies that affect the final product. Without strict process control, minor deviations can accumulate, resulting in defective units that require rework or scrapping.
2. Human Errors in Quality Control
Quality control teams are responsible for identifying defects before products reach customers, but manual inspections are not foolproof. Human fatigue, oversight, and limited inspection time make it difficult to catch every defect. Additionally, when production volumes are high, quality checks become rushed, increasing the likelihood of defective products being shipped. Businesses relying solely on manual quality control often struggle to maintain consistent product quality.
3. Poor Supplier Quality Management
Many companies source raw materials and components from third-party suppliers. If suppliers fail to meet quality standards, defects can enter the production line undetected. Inconsistent supplier quality leads to variations in product performance, increased rework, and higher return rates. Without an effective supplier management system, businesses face challenges in ensuring uniformity across production batches.
4. Lack of Real-Time Monitoring
Defects often go unnoticed until later stages of production or even after products are in the hands of customers. Delayed defect detection leads to costly recalls, warranty claims, and damaged customer trust. Businesses that lack real-time monitoring systems struggle to identify defects early, making corrective actions reactive rather than preventive.
5. Inadequate Data Utilization
Many businesses collect large volumes of production data but fail to use it effectively. Without advanced analytics, identifying patterns in defect occurrences becomes difficult. Companies that rely on outdated reporting methods miss valuable insights that could help improve production processes and reduce defects.
How Software Can Help Businesses Reduce Product Defects
1. Automated Quality Control and Inspection
AI-powered defect detection software eliminates human error by automating quality inspections. Machine vision systems equipped with deep learning algorithms can analyze products in real-time, identifying defects that human inspectors might overlook. These systems scan thousands of units per minute, ensuring a higher level of accuracy and consistency.
Automated quality control software also integrates with existing manufacturing equipment, allowing for real-time defect detection at different production stages. By catching defects early, businesses can prevent faulty products from moving further down the supply chain, reducing rework costs and improving overall efficiency.
Moreover, manufacturers can improve design accuracy by using tolerance analysis software to ensure that parts fit together correctly, reducing the chances of defects caused by dimensional variations.
2. Predictive Analytics for Defect Prevention
Predictive analytics software uses historical production data and machine learning models to anticipate defect trends. By analyzing past defect patterns, the software identifies potential problem areas before they escalate. This allows manufacturers to adjust production parameters, optimize processes, and proactively address issues before defects occur.
For example, if a production line consistently produces defects at a specific machine station, predictive analytics can pinpoint the issue and recommend corrective actions. Businesses that leverage predictive analytics reduce defect rates, lower production costs, and improve product reliability.
3. Standardizing Manufacturing Processes with AI
Manufacturing process control software ensures consistency across production lines by monitoring equipment performance, material properties, and operator actions. AI-driven solutions adjust machine settings in real time to maintain optimal production conditions, reducing variations that lead to defects.
For instance, if a material inconsistency is detected, the software can automatically adjust machine parameters to compensate, ensuring that the final product meets quality standards. Standardized processes lead to fewer defects, higher production efficiency, and reduced waste.
4. Supplier Quality Management Software
To ensure that incoming materials meet quality standards, businesses use supplier quality management software. These systems track supplier performance, analyze defect rates, and enforce compliance with quality requirements. If a supplier consistently delivers subpar materials, the software flags the issue and recommends corrective measures.
Advanced supplier quality management tools also use blockchain technology to enhance traceability. By maintaining an immutable record of material sourcing and quality inspections, businesses can ensure that only high-quality inputs enter production.
5. Real-Time Defect Monitoring and Alerts
One of the biggest advantages of defect detection software is real-time monitoring. Unlike traditional quality control methods that detect defects only at the final inspection stage, modern software solutions identify issues as soon as they arise in production.
IoT-enabled sensors and AI-powered cameras continuously analyze product dimensions, surface quality, and functional attributes. If a deviation from acceptable parameters is detected, the system immediately sends alerts to operators and production managers. This real-time feedback loop ensures that necessary adjustments are made on the spot, reducing the number of defective units before they reach the final stage.
Real-time monitoring also helps in trend analysis. If a particular defect is recurring at a specific stage, manufacturers can pinpoint the root cause and take corrective action. This prevents future defects and improves overall process efficiency.
6. Root Cause Analysis and Process Optimization
Finding the root cause of defects is critical for long-term quality improvement. Without proper defect tracking, manufacturers may end up fixing symptoms instead of the underlying problem, leading to repeated quality issues. Defect analysis software uses AI and statistical modeling to identify patterns in production failures and trace them back to their source.
For example, if a manufacturer notices that a particular batch of products has alignment issues, root cause analysis software can assess various factors such as machine calibration, material consistency, and temperature variations. Once the main cause is identified, manufacturers can adjust machine settings, retrain workers, or modify raw material specifications to prevent defects from occurring again.
Process optimization features also help manufacturers refine production workflows. By analyzing defect frequency and location, businesses can eliminate inefficiencies and reduce unnecessary steps in the manufacturing process. This leads to higher productivity, lower defect rates, and improved profitability.
7. Digital Twin Technology for Defect Reduction
Digital twin technology is revolutionizing quality management by allowing manufacturers to create virtual replicas of physical production lines. These digital models simulate real-world manufacturing processes, enabling businesses to test different scenarios and identify potential defect sources without disrupting actual production.
With AI-driven digital twins, manufacturers can simulate tolerance variations, analyze the impact of different machine settings, and experiment with alternative materials. If a simulation shows that a particular setting leads to defects, adjustments can be made in the real production line before problems arise. This predictive approach minimizes production risks, ensuring that only high-quality products are manufactured.
8. Customizable Quality Control Parameters
Every industry has unique quality requirements, and a one-size-fits-all approach does not work for defect detection. Modern quality management software allows businesses to set custom parameters based on industry standards, customer requirements, and internal quality benchmarks.
For example, in the automotive sector, defect detection software can be configured to assess factors such as welding precision, paint thickness, and assembly accuracy. In the electronics industry, software may focus on circuit integrity, component placement, and thermal performance. Customizable settings ensure that manufacturers meet regulatory compliance while maintaining high product standards.
9. Reducing Costs Associated with Product Defects
Product defects are not just a quality issue; they have a direct impact on a company’s bottom line. Businesses that fail to address defects face increased material costs, higher labor expenses, and expensive warranty claims. Implementing software-driven defect detection significantly reduces these financial burdens.
Material costs decrease as scrap rates go down. Since defect analysis software catches issues early, fewer raw materials are wasted on unusable products. Labor costs also decrease because workers spend less time fixing defective products or performing rework. Instead, they can focus on core production tasks, improving overall efficiency.
10. Integrating Defect Detection Software with ERP and MES Systems
Modern defect detection tools are designed to work seamlessly with Enterprise Resource Planning (ERP) and Manufacturing Execution Systems (MES). This integration provides a comprehensive view of production quality, linking defect data with supply chain management, inventory tracking, and production planning.
For example, if defect detection software identifies recurring issues with a specific batch of raw materials, ERP integration allows manufacturers to trace the source and notify suppliers. If a machine consistently produces defective components, MES integration can automatically schedule maintenance or recalibrate settings.
By integrating quality management software with existing production systems, businesses gain a holistic approach to defect prevention. This level of coordination reduces delays, improves decision-making, and ensures that all departments work towards a common goal of quality excellence.
Conclusion
Product defects remain a major challenge for businesses, but modern defect detection software provides an effective solution. From real-time monitoring and AI-driven quality control to predictive analytics and digital twins, advanced software solutions help manufacturers reduce defects, improve efficiency, and lower production costs.
By implementing automated quality control, businesses can catch defects before they reach customers, avoiding warranty claims and brand reputation damage. Root cause analysis software ensures that problems are permanently fixed, while process optimization tools streamline production workflows. Integrating defect detection software with ERP and MES systems further enhances efficiency and supply chain management.