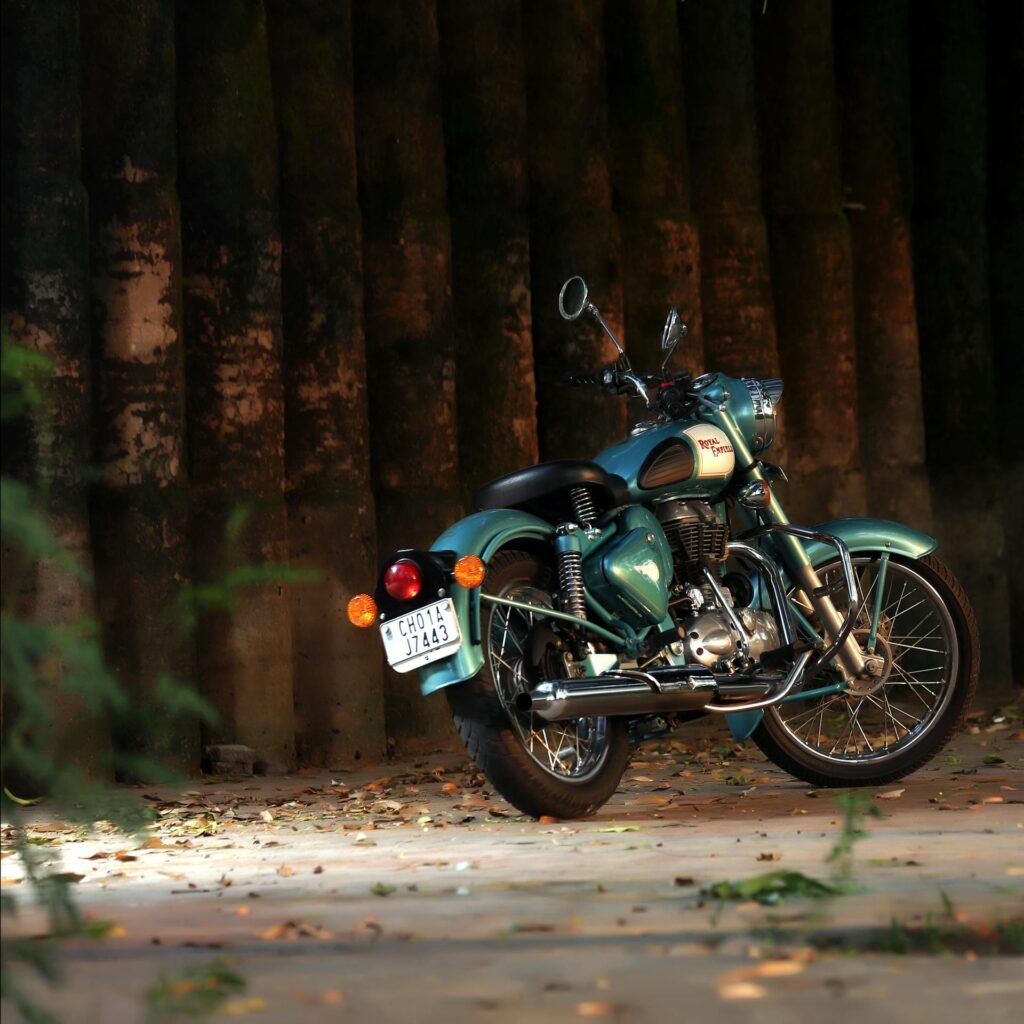
Various industries play a significant role in using reciprocating pumps due to their efficiency and flexibility. These pumps are widely used to move various types of fluids and are best known for converting mechanical energy into hydraulic energy. Learning how they work and understanding their benefits can help companies optimize processes.
Sublimation of Reciprocating Pumps
A reciprocating pump, or piston pump, transfers liquid through a simple mechanism. Based on the principle of a piston or plunger reciprocating inside the cylinder, this pump builds up pressure to transport fluid. This motion is similar to that of a bicycle pump, where the piston moves in and out to take in and expel air.
Key Components
There are several key components in reciprocating pumps that make their operation possible. These include the cylinder, piston or plunger, valves, and crankshaft. Each component plays a specific role in ensuring the pump operates smoothly. The piston moves up and down inside the cylinder. The cylinder also contains the valves that control the entry and exit of fluid. The crankshaft rotates and is powered by a motor (although not a conventional device, it is the movement of the piston that drives this action).
How It Works
Reciprocating pump operations are carried out step-by-step. The motion of the piston first creates a vacuum in the cylinder, causing fluid to enter through an inlet valve. The piston then moves forward, compressing the fluid and increasing the pressure. This pressure forces the fluid out via an outlet valve, driving it into the system or application. The fluid is pumped through a vein, and the cycle begins again, ensuring a continuous fluid flow.
Types of Reciprocating Pumps
Different categories of reciprocating pumps are available, each designed for specific requirements. Piston pumps and plunger pumps are the most common. Piston pumps are a good fit for applications with moderate pressure and flow requirements, while plunger pumps excel in high-pressure applications. Diaphragm pumps are also used for applications that require pure fluids, as the diaphragm prevents fluid contact with mechanical components.
Advantages of Reciprocating Pumps
Reciprocating pumps offer numerous advantages, making them ideal for use in oil and gas, chemical processing, water treatment, and other industries that involve high-pressure applications. These pumps are known for their accuracy in flow control, which is crucial when applications require precise metering of fluids. Their rugged design makes them highly durable and reliable, ultimately leading to reduced maintenance costs.
Use Cases Across Industries
Given their versatile nature, reciprocating pumps are utilized across several industries. In the oil and gas industry, they are used to transfer crude oil and natural gas. Chemical processing facilities use them to transport viscous and corrosive liquids. In wastewater treatment facilities, reciprocating pumps effectively handle sludge and slurry. The common use of these pumps can be attributed to their adaptability to various fluid types and conditions.
Challenges & Considerations
While reciprocating pumps offer many advantages, they also face some challenges. The design includes moving parts that can wear out over time. It’s important to consider regular maintenance whenever changes are made to your system. Additionally, the pulsating flow nature of reciprocating pumps may require extra accessories like pulsation dampeners to reduce pulsation and prevent damage to the system.
Some Maintenance Tips to Make It Last
Regular checks of valves, pistons, cylinders, and other components are essential to prevent issues in maintaining a reciprocating pump. Friction and wear can be reduced by lubricating moving parts. Regular inspection of the pump and timely correction of deviations can help extend its lifespan. A consistent maintenance schedule can minimize downtime and improve efficiency.
Emerging Trends in Reciprocating Pump Technology
Technological advancements continue to improve reciprocating pumps’ performance. Key materials and design innovations focus on reducing wear, enhancing performance, and improving energy efficiency. Automation and smart monitoring systems are integrated into reciprocating pumps to provide real-time data, predictive maintenance, and minimal operational disruption.
Conclusion
Reciprocal pumps’ versatility and efficiency influence diverse industries. To optimize their processes, businesses should understand how they work, their components, and how they can benefit from using them. Despite the challenges, regular maintenance and evolving technologies ensure that reciprocating pumps remain at the forefront of industrial applications. They continue to play a vital and characteristic role in industries, even as they evolve to meet the demands of a dynamic world.