
Recycling, you won’t fail to have noticed, is big business. Beyond the obvious environmental benefits of reusing stuff, raw materials are pricier than ever – especially the hard-to-find (and process) stuff that goes into the production of each and every modern motor car. Throw in additional expensive commodities like batteries, and it’s little wonder that the days of manufacturers regarding end-of-life vehicles as someone else’s problem are fading fast. The cost of recycling is increasingly outweighed by the benefits.
Almost certainly that is the justification for Toyota launching itself at the concept of re-purposing, re-manufacturing and recycling with unprecedented gusto. You know it’s important because the firm has bestowed upon it a snappy new name – Toyota Circular Factory – although the title does signify two things: firstly, that the processing is taking place at existing production facilities, and secondly, that it is intended to occur at significant scale. Kicking off at Toyota Motor Manufacturing UK’s Burnaston plant – the first such operation globally – it expects to get through 10,000 cars a year.
The process, which takes place alongside the business of building new Corollas, is focused on three key areas: re-usable parts, items that can be re-manufactured and materials fit for recycling. The first will be reintroduced to the market via dealers or parts suppliers; the second – which includes batteries – will be assessed for future re-purposing; the third involves Toyota harvesting as much copper, aluminium, steel and plastic as possible and using them to replace ‘virgin’ materials in the production of new vehicles.
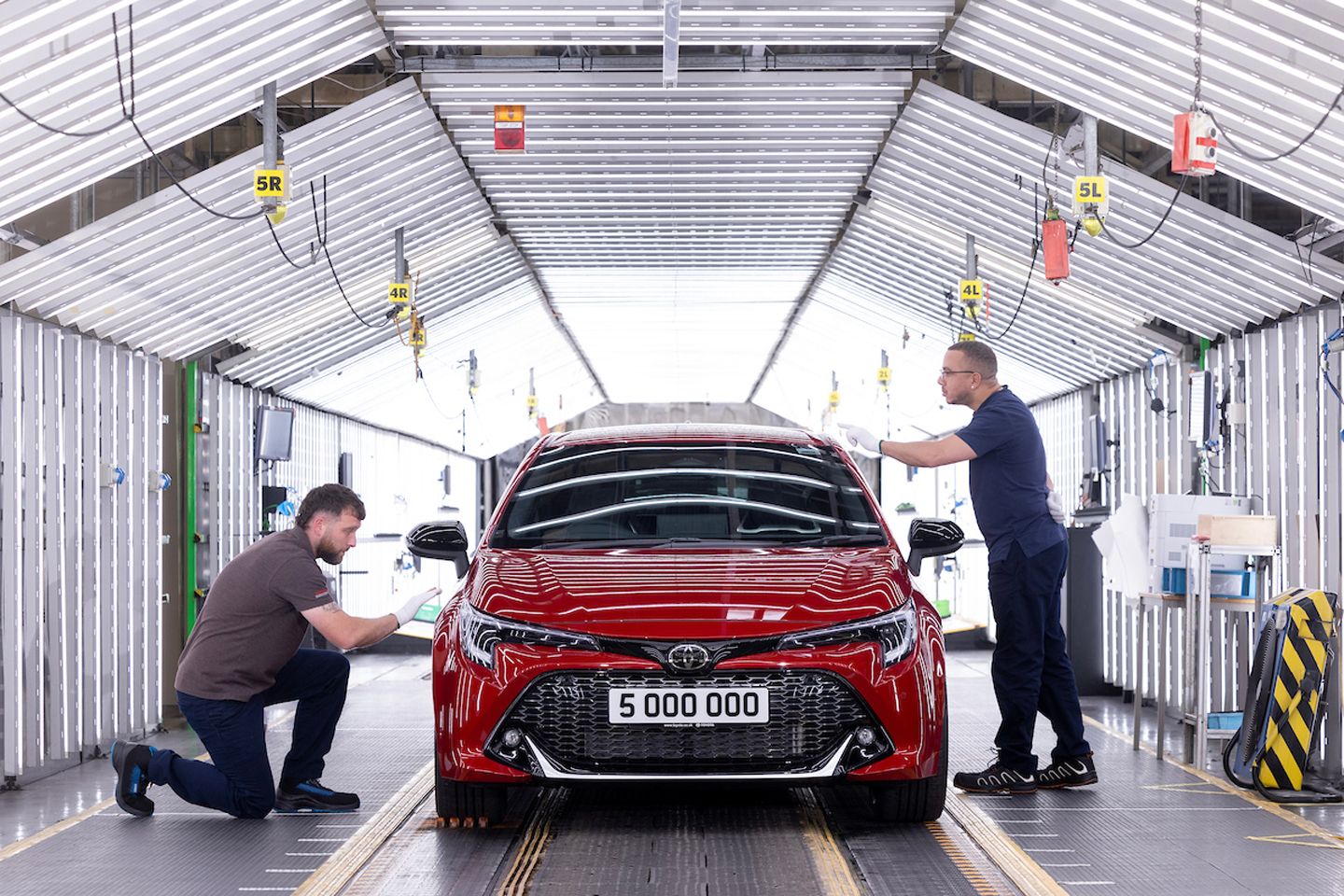
“We initially anticipate recycling around 10,000 vehicles a year in our UK facility, which will give new life to 120,000 parts, recover 300 tonnes of high purity plastic and 8,200 tonnes of steel – amongst other materials,” said Leon van der Merwe, Vice President of Circular Economy at TME.
“As a next step for the Toyota Circular Factory concept, we plan to roll out similar operations across Europe. And we’re not stopping at our own facilities – we are eager to collaborate with other organisations who share our passion of circularity and commitment to carbon neutrality.”
Toyota hasn’t said exactly how the physical operation fits into the space and logistical jigsaw that is a busy car factory, nor how many employees it will involve – but it has said it ‘will begin activities in the third quarter of this year’, suggesting that plan is well underway (comments from those in the know at TMUK very welcome below). Certainly the manufacturer expects Burnaston, which celebrated building Toyota’s five-millionth UK-assembled car last year, to become a centre of excellence as it pioneers the new initiative.