✕
Hydrogen as a source of energy has become a major focal point of discussion within the energy transition, thanks in large part to its high energy density by mass and ability to be produced without emissions from readily available resources, like water and renewable electricity. The foundation for utilizing hydrogen as a fundamental aspect of the energy transition is being built today through cutting-edge technology development, and first movers who are paving the way for hydrogen’s essential role in decarbonizing hard-to-abate sectors. There are a variety of applications that electrification will struggle to address, and that is where the adaptation of hydrogen as a fuel will be critical to execute through the partnership of producers, application OEMs (Original Equipment Manufacturer), and EPCs (Engineering, Procurement and Construction). As a supplier to the hydrogen market for more than 65 years, Air Products brings an industry-leading perspective on the expanding hydrogen value chain. Specifically, this article will focus on the road to hydrogen’s adoption within the energy mix for both electricity and heating generation, while focusing primarily on stationary combustion applications within industrial settings.
Applications: How is hydrogen being used?
Fuel cells are often touted as the high efficiency application to most effectively utilize hydrogen to its greatest energy potential, but hydrogen can be equally as effective when used in combustion applications under the proper circumstances – OEMs are also developing stationary combustion engine equipment that can leverage decades of thorough development and refinement by comparison to the burgeoning fuel cell industry. Whether choosing a fuel cell or a combustion engine for an onsite generator, each application can be an effective way to leverage hydrogen as a source of backup electricity, especially within industries that need to ensure uptime through layers of energy redundancy. Hydrogen will also have a place in large-scale power generation through peaker turbines, first as an agent to help turndown and startup efficiency, and progressively as a higher percentage of the overall fuel blend used for flex capacity needs.
Power generation utilizing hydrogen is in the spotlight for both the mobility and stationary markets; however, the potential heating applications of hydrogen are just as prominent and necessary in the energy transition. In particular, introducing hydrogen into industrial and commercial boiler systems has shown promise as a likely first mover heating application. A strong advantage of hydrogen over electricity as a renewable energy source is that it is generally easier to retrofit into existing boilers and heating systems. Water tube boilers, in particular, which see widespread use in heavy industry (chemicals, refining, and paper) and commercial services (universities and hospital networks) alike, are high pressure and temperature applications, will need an energy source other than electricity to achieve their ideal operating conditions. Starting with hydrogen-natural gas co-firing also provides these customers a stepwise approach to decarbonization, without significant upfront investment to upgrade their equipment and supporting infrastructure.
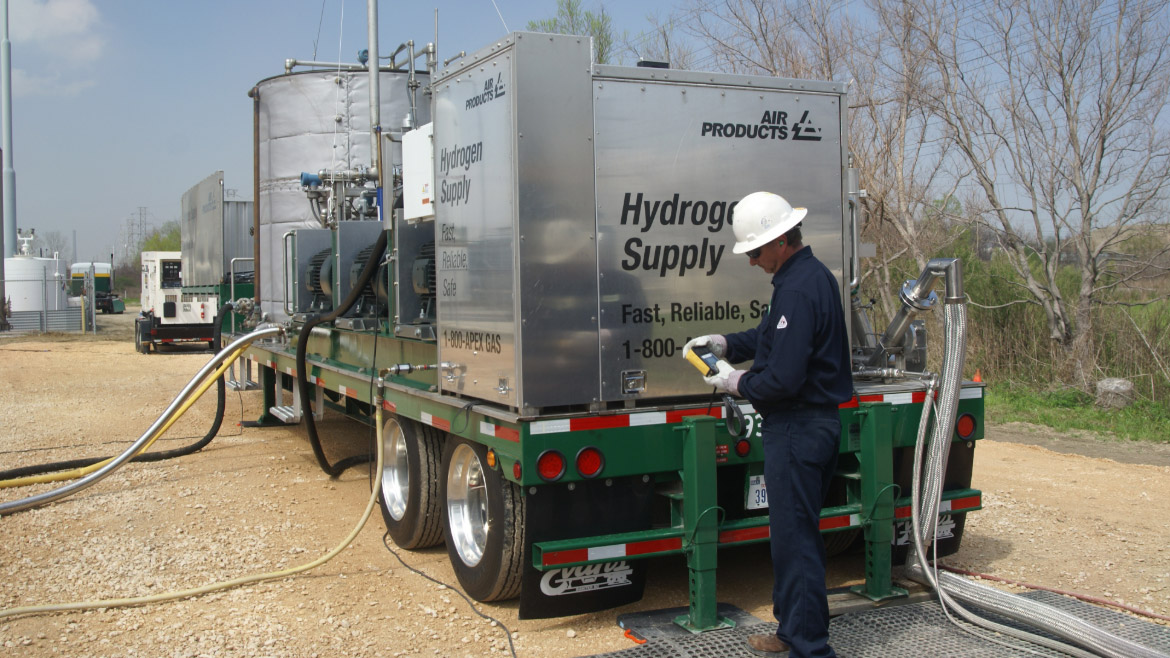
CO-FIRE: Co-firing and blending is a natural first step toward the goal of full adoption.
Supply Scenarios: What is the usage profile of the hydrogen?
As a result of hydrogen’s traditional uses in space flight, refining, and chemicals applications, robust supply chains have been established over the past several decades. Established hydrogen suppliers will be able to provide onsite/pipeline solutions, distributed product in cryogenic trailers or pressurized tube trailers, and emergency backup or supplemental supply for high run-rate periods. Of course, every facility’s adoption of hydrogen will provide unique operability considerations that may require trials, co-firing/blending at the customer site, and batch supply of hydrogen before full adoption. Directionally, large scale and continuous hydrogen uses will require collocated onsite/pipeline integration, which may also include supplemental onsite storage depending on the uptime and redundancy requirements of the process. Distributed hydrogen through trailers is ideal for early adoption and scale-up of various applications, such as gradual introduction through co-firing within existing infrastructure, as well as up to full adoption for certain boiler scales and backup power generation. The supply chain would not be complete without the ability to serve customers in emergency and flexible high-runtime periods, which is what the hydrogen industry currently achieves with its traditional customer base today and will seek to adapt to its evolution as a fuel source in the energy industry moving forward.
Changing a facility’s energy source is not a trivial task, but the right hydrogen partner can help scope out your facility to take into consideration hydrogen-specific NFPA and OSHA requirements, while simultaneously providing a pathway to incrementally introduce hydrogen over-time to ensure safe adoption without process interruption. From testing and trials, all the way to full adoption and continuous use, the hydrogen industry is equipped to transition new users over time based on their respective decarbonization profiles.
Phasing: How will hydrogen be introduced and expanded over time?
Hydrogen still has a long way to go to develop into a comparable fuel to the fossil fuels it is replacing, both from a technical and economic perspective. Co-firing hydrogen with natural gas, or pre-blending on-site through a blending skid, is a growing trend that allows first movers to incrementally reduce their carbon intensity without investing additional capital, while simultaneously providing concrete data and experience of how hydrogen will react within the corresponding process. This avenue of adoption can be started today, and many companies across industries have already conducted trials of low-ratio (<30% by volume) hydrogen blends within natural gas combustion equipment.
The introduction of hydrogen through co-firing and blending is a natural first step toward the goal of full adoption, with the next level of adoption involving equipment retrofits to increase the hydrogen ratio, and finally the incorporation of new equipment aimed to utilize hydrogen at 100% concentrations to its full potential. Hydrogen is a key piece of the decarbonization puzzle that will add value across a variety of different industrial processes, and the roadmap can be adjusted to meet a phased approach that matches the emissions reduction ambitions of those that are striving to generate a cleaner future.