✕
The state of education in the HVACR industry is perhaps more important than ever before. The way of the world has placed more of an emphasis on educating technicians, contractors, and those alike, with a heightened focus on trends like energy efficiency, smart controls, and refrigerants.
As technology and the industry as a whole continue to evolve at a rapid rate, the education surrounding it must as well. Educators must also work to ensure they are meeting industry demands, have enough training to go around, and that they are aiding in securing recruits.
To do this, educators have to stay up-to-date, learn how each specific student learns best, discover the best ways to conduct these trainings (whether it be hands-on, virtual, or a mix of both), and always look forward.
Trends in Education
The biggest trends in the education sector these days revolve largely around decarbonization and electrification. Additionally, smart controls, more hands-on training, and new-generation refrigerants are at the forefront of educators’ minds.
“For example, inverter-controlled systems, including high-performance heat pumps, are becoming increasingly popular, even in geographic areas that traditionally did not embrace conventional heat pump equipment,” said Eugene Silberstein, national programs director of HVAC Excellence. “More and more programs are incorporating A2L refrigerant training into their programs as the phasedown of refrigerants with high-GWP continues.”
Training organizations understand these significant emphases, and thus, have incorporated best practices into their curriculum.
HVAC U, a training organization whose mission is to empower individuals by delivering high-quality technical training that enhances both competency and capacity, has some beneficial tools that help educate their techs. One of them is liDAR, which utilizes pulsed lasers to accurately and constantly measure distances to a given target or area.
“This technology uses sensors that enable light-based measurement and mapping tools, which we can use to quickly measure rooms and help us perform load calculation,” said Brynn Cooksey, owner and general manager of Air Doctors Heating and Cooling in Belleville, Michigan, and also the founder of HVAC U. “Commissioning tools also help us prove the equipment’s installed capacity and efficiency. Proper design and commissioning are now required in many areas of the United States.”
Using resources that are already available to technicians can also assist technicians in grasping concepts earlier than expected — another thing that educators have been noticing.
“The biggest thing that I’ve noticed is that it’s not taking as long for someone who’s just getting started in the trade to actually be able to work with their hands … especially in a highly hands-on and book-educated training program,” said Jesse Stewart, national training manager at NAVAC. “And that’s a really good point, considering the skill gap. If we can’t fill the skill gap, then we’re just going to be chasing our coattail for the rest of our lives.”
Recruitment
Fortunately, there seems to be more than enough training to go around to ensure every technician in the industry is educated. It’s making sure there are enough technicians to educate that poses a challenge — not that availability of training doesn’t vary state-by-state.
“There have been quite a few states I’ve been to that have what seems like more than enough training programs, especially with the amount of time and effort that goes into them … and there have been some states where they just put on a three-month certification program that gets them an Environmental Protection Agency (EPA) 608, and they say that they’re ready to work.”
Silberstein said very few HVACR training programs are completely full with long wait lists for enrollment in future class starts.
“Having said that, programs with available seats is an indication that more can be done to recruit more students into the industry,” Silberstein said.
The HVACR industry arguably has one of the most significant skill gaps in the country compared to other occupations. And, a lot of other occupations are after the same pool of talent that the HVACR industry is after. So, to bring them into HVACR, educators need to start reaching the younger workforce to increase the chances of combating the workforce shortage.
“HVAC contractors and other organizations should actively work with their local school systems to provide a clear path for students and parents to enter the trades,” Cooksey said. “We also need to market the skilled trades as a ‘Plan A’ alternative that is an equally successful path to an academic college.”
To bring students to his university, Cooksey has developed relationships with various organizations that specialize in workforce development. They’ve also leveraged relationships with local schools and incorporated their curriculum with various training, so that students can pursue higher education if they so choose to continue their trade studies.
“The big thing with recruitment is giving the student options so that they can plan a path for their career,” Cooksey said. “Additionally, we have to make the trade appealing to them. Students need to know they can earn a substantial income and have a fulfilling career.”
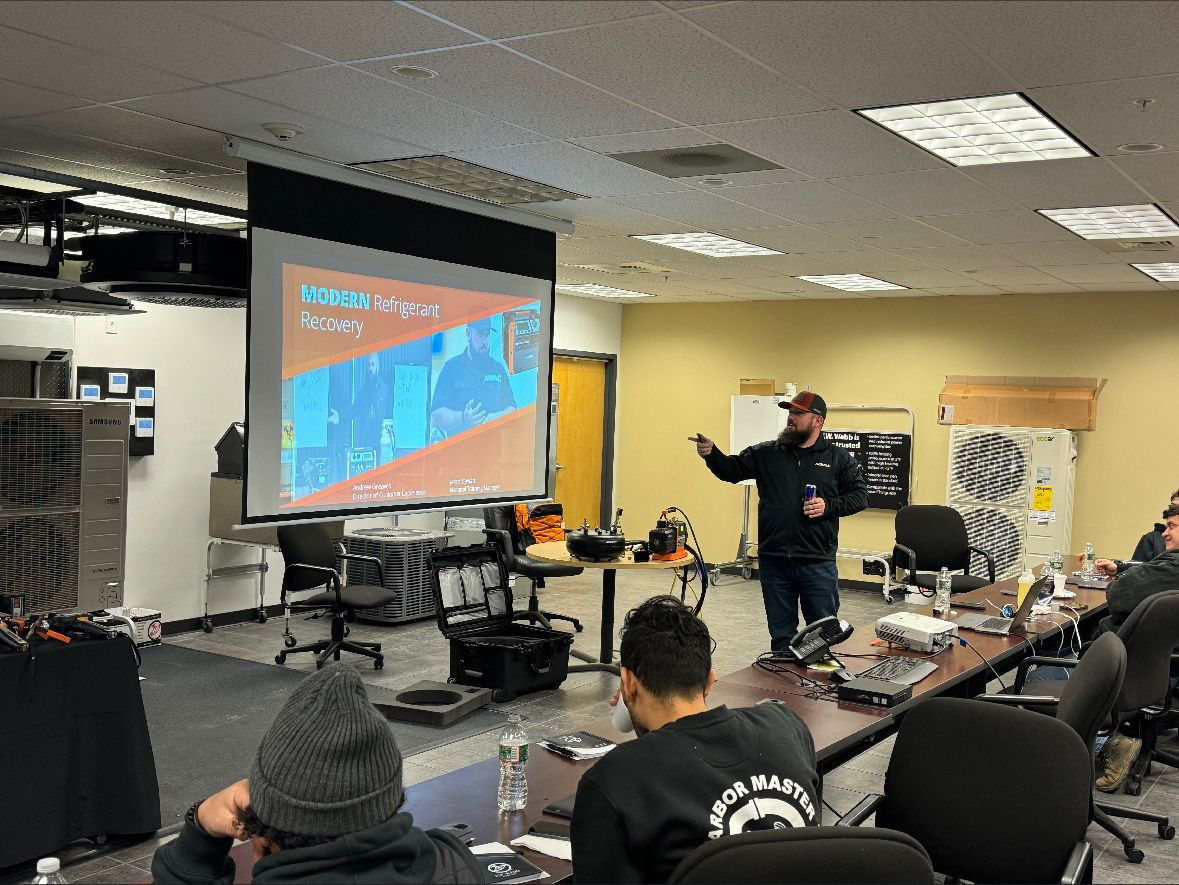
ABILITY: One of the biggest things to realize about HVACR education is today’s technicians have the internet at their disposable. (Courtesy of NAVAC)
And making HVAC appealing is really half (if not more) of the battle.
Stewart said the biggest thing he’s found that’s helped bring students to the trades is to show them that this industry is not “death by PowerPoint or death by book.”
“Show them this is hands-on,” Stewart said. “Incorporate something to where your students can actually work in the community nearby to help provide a benefit to them and the community and get the community support to help push your program.”
It’s important to note that recruiting students into HVACR is not just the job of an educator. It’s everyone’s responsibility to actively recruit. whether it’s from high schools, community colleges, or organized labor organizations. While some in the industry might say it’s the job of an educator, schools often have said that it’s the responsibility of contractors and industry groups to be at the forefront of these recruitment efforts.
“With limited resources and availability, the faculty and staff at HVACR training programs simply do not have the bandwidth to shoulder the recruitment burden,” Silberstein said. “The employers of program completers can help alleviate this burden while, in the long run, helping themselves. They are, at the end of the day, the benefactors of the skills that training program completers possess.”
What local HVACR training programs today can do is present a fertile ground for harvesting already existing talent that has, in some way, already committed to the HVACR industry.
“By engaging with program advisory committees, for example, employers can help shape the future workforce by participating in the processes that affect the quality, content, and efficacy of the training and education students receive,” Silberstein said. “By creating partnerships with educational institutions, employers can establish a pipeline of talent tailored to their specific needs, ensuring a seamless transition from classroom to career.”
Training Types
It’s one thing to know how to accomplish a task, but having the necessary hands-on skills to perform these tasks is something completely different. The most effective training programs combine the two.
“Highly effective HVACR training programs incorporate both classroom learning and hands-on experiences to ensure that program completers have the retained knowledge required for industry success as well as the ability to perform the numerous physical tasks that are required to keep our systems running as effectively and efficiently as possible,” Silberstein said.
Hands-on learning is a cornerstone of cultivating an effective HVACR education.
“The combination of theoretical training and practical application not only enhances understanding but also ensures that the knowledge is retained for a longer period,” Cooksey said. “This approach is instrumental in preparing the next generation of HVAC professionals.”
In Stewart’s personal opinion, training should consist of 60% hands-on and 40% books and literature. But, not every student learns the same way. It’s not necessarily a one-size-fits-all solution.
“You have to make time to support your students,” Stewart said. “At the end of the day, we educators — in a strange kind of sense — are product managers. Our products are the students that we produce, and we want to produce high-quality technicians. Each individual student will require a certain amount of attention … and so you have to make time to make sure that everyone has an equal opportunity.”
Even though a trend seems to be that technicians are grasping things a lot quicker, that’s with a lot of hands-on learning coupled with on-the-job training and book education.
“The biggest thing for any training program is to remember that this generation of technicians has the ability to be the best there ever was, because they have the internet in their back pocket,” Stewart said. “So, encourage your students to invest in themselves and invest time in learning this trade outside of their 9-5 or regular learning hours.”
Educators should also be enforcing their local codes into their education curriculums so that way the techs going out to in the field to do this hands-on work know things like what’s legal or not, what can get fined, and what licenses are required.
Regulations and Evolutions
New regulations and evolving technology, as aforementioned, affect the education sector of HVACR — but not necessarily in a negative way.
According to Stewart, if anything, these things can have a positive effect.
“The biggest thing a trainer can do to be a really good trainer, is the ability to listen and learn,” Stewart said. “A lot of people think that as trainers and educators, we know everything. There’s not a single person that I know that’s in this industry that will tell you they know everything. So, these new codes regulations — especially when you get down to the state level — they just add an additional value to the programs that we’re building across the country.”
Once a new technology or regulation is introduced, all technicians have to be re-educated to maintain their effectiveness. And in order for that to happen, educators themselves must know enough about them to effectively convey this information to their students. After all, teachers can’t teach what they don’t know.
“This requires that instructors receive targeted professional development in these areas. … If students don’t learn about a particular technology, how can they possibly be prepared to work on it?” Silberstein said. “If students are ill-equipped to work with a particular technology and have limited, or no, retained knowledge of the technology, their ability to secure viable employment might be greatly reduced.”
And the updates the industry has seen are plentiful — ratings from the Air-Conditioning, Heating, and Refrigeration Institute, new refrigerants, and other efforts to increase energy efficiency.
“As technology changes, technicians will need to continue their education to stay abreast of the ever-changing industry,” Cooksey said. “From the standpoint of a training organization, there needs to be a pathway for students who have completed programs to come back to class for these updated training sessions to stay current with industry trends. The need for updated training is urgent and cannot be overstated.”
This is especially important when currently many instructors are being asked to teach technologies that they themselves have never encountered during their time in the field.
Transitions
One of the biggest things currently facing the education sector is the transition to A2L refrigerants. However, for the most part, the transition is being approached by educators with wide-open arms.
“Because if there is one thing that educators will tell you … is this isn’t the first refrigerant transition we’ve seen, and it’s probably not going to be the last,” Stewart said. “That’s the most exciting thing about this trade — nothing stays the same for very long. But, it’s provided us with opportunities to work with people like the ESCO Institute and collaborate to bring their educational programs into our training centers and programs, to provide the most accurate information to the students; and also to help eliminate a lot of the fear.”
When people hear “slightly flammable,” it’s understandable that a little panic might ensue. But according to educators, there are a lot of myths that need to be debunked.
“There is a lot of false information about A2Ls and their use,” Cooksey said. “Some refrigerant manufacturers explicitly targeted educators to communicate the proper information and refrigerant-handling best practices. Many resources are available so that educators can train the workforce. It will be a similar rollout to R-410A. Everyone was anxious for a while regarding its higher operating pressures, but once the systems were installed and more professionals became used to this, the change became less important.”
Regarding the specific training required to handle refrigerants safely, the best field and service practices already in place for the refrigerants currently being utilized can be applied to the new refrigerants.
“There are, however, some additional considerations that field personnel must be aware of,” Silberstein said. “These include, but are not limited to, refrigerant storage, system labeling and marking, mitigation requirements, installation and piping requirements, tool and instrument requirements, and other safety-related concerns.”
As of today, there is no nationwide requirement for training on the new A2Ls. EPA 608 still covers technicians being able to handle the new refrigerants.
“However, I would like to stress that I do know of some states that are requiring things like the ESCO Institute’s low-GWP refrigerant certification at a distributor or even some at a city or town ordinance level, before they’ll even allow you to purchase or handle the refrigerant or the equipment,” Stewart said.
Looking Ahead
When educators in the HVACR industry look ahead to the next year they see excitement, greatness, change, and prosperity.
“With certain products being incentivized, contractors, manufacturers, distributors, and training organizations should all benefit from increased sales from energy-efficient incentives,” Cooksey said. “This positive outlook for the industry should inspire confidence in our collective future.”
Stewart said the upcoming year is going to be a fantastic time for educators, especially in light of the A2L transition, because it means that what’s coming is more information that will skyrocket facts to the forefront.
“I do believe that in 2025 and up until 2026, we’re going to actually see some of the biggest changes in the information that we’ve been given and actually get some solid info to produce to our training departments, students, and programs. … It’s no longer going to be these myths or these videos or these poor HVAC forms that are going to cause students to think that they’re getting ready to work around something dangerous,” Stewart said. “It’s our job as educators to provide facts, not theories.”
Now that many skeptics have come to terms with the fact that new-generation refrigerants are here to stay, the industry can move forward as a whole.
“When we all pull on the same end of the rope, it takes far less energy to accomplish a great deal,” Silberstein said. “Although industry stakeholders might have different opinions on any number of topics, the bottom line is that we all want to see our industry succeed and will, at the end of the day, do what needs to be done to ensure a bright and successful future for it.”