Determining accurate equipment costs is crucial for construction project success and profitability. Construction managers must consider various factors to calculate the total equipment expenses, from ownership costs to daily operational expenses.
Heavy Equipment Rental: A Flexible Solution
Business owners who utilize heavy construction equipment rental often find it offers flexibility and can be more cost-effective for shorter projects or specialized tasks. When calculating rental costs, consider the daily, weekly, or monthly rates offered by equipment providers. These rates typically include basic maintenance, but operators, fuel, and transportation usually incur additional charges. Remember to factor in insurance coverage and security deposits required by rental companies. The total rental period should include both active use days and any potential weather delays or project extensions.
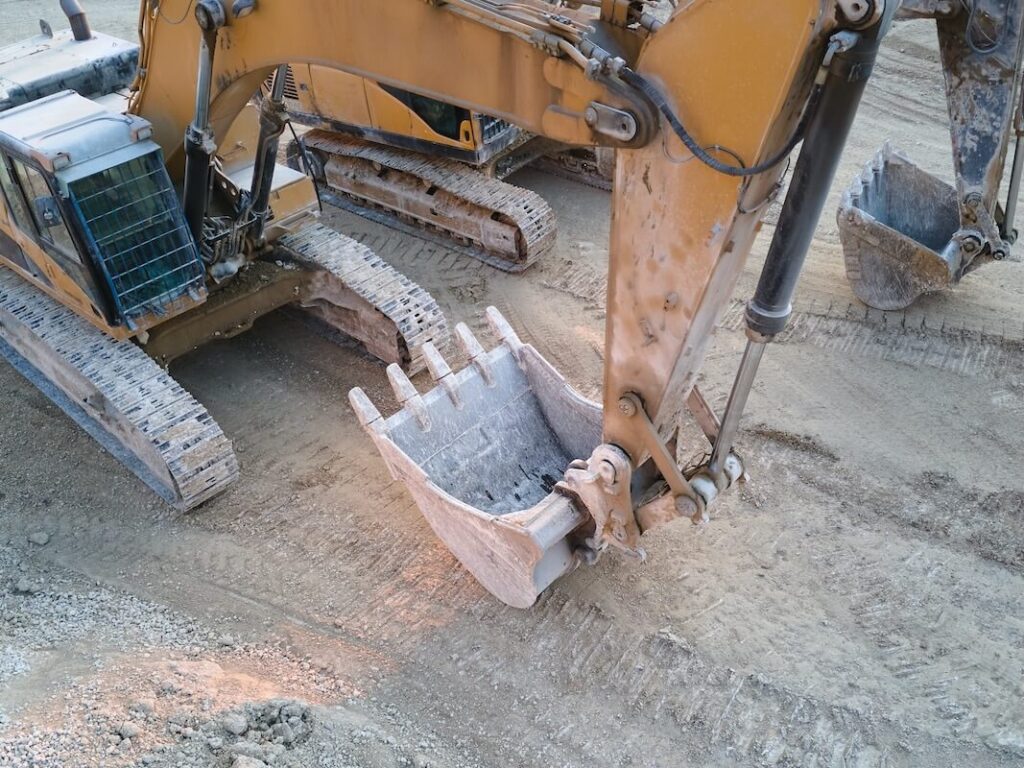
Ownership and Operating Costs
For companies that own their equipment, the cost calculation becomes more complex. Initial purchase price, depreciation, insurance, taxes, and storage facilities all contribute to ownership costs. Operating costs include:
- Fuel consumption and current fuel prices
- Regular maintenance and repairs• Operator wages and benefits
- Lubricants and filters
- Tire replacement or track maintenance
Equipment Life Cycle Analysis
Understanding the equipment’s life cycle is essential for accurate cost projections. Most heavy machinery experiences declining productivity and increasing maintenance costs as it ages. Construction managers should track equipment performance and maintenance history to determine optimal replacement timing. This analysis helps balance the costs of keeping older equipment operational against the investment in new machinery.
Transportation and Mobilization Expenses
Moving heavy equipment between project sites significantly impacts overall costs. Transportation expenses include fuel, permits for oversized loads, escort vehicles when required, and potential road closure fees. The time spent loading, securing, and unloading equipment must also be factored into the total cost calculation.
Maintenance Planning and Cost Control
Effective maintenance programs help minimize unexpected breakdowns and extend equipment life. Scheduled maintenance costs should be calculated based on manufacturer recommendations and usage patterns. This includes routine inspections, oil changes, filter replacements, and component updates. Emergency repairs typically cost more than planned maintenance, so building a contingency fund for unexpected issues is advisable.
Project-Specific Requirements
Different projects demand varying levels of equipment utilization. Calculate equipment costs based on:
- Expected working hours per day
- Project duration and timeline
- Site conditions that might affect equipment performance
- Local regulations regarding equipment operation
- Backup equipment needs for critical operations
Technology Integration Costs
Modern construction equipment often includes advanced technology systems. When calculating equipment costs, consider:
- GPS and telematics systems fees
- Software subscriptions
- Training costs for operators
- System maintenance and updates
- Data management expenses
Insurance and Risk Management
Equipment insurance is a significant cost component that varies based on equipment type, value, and usage. Proper coverage protects against theft, damage, and liability claims. Risk management costs might include security systems, operator training programs, and safety equipment. Companies should also consider specialized insurance riders for equipment operating in high-risk environments, such as marine construction or demolition projects. Insurance providers often offer discounts for implementing comprehensive safety programs and maintaining detailed maintenance records, which can help offset the overall cost of coverage.
Future Cost Projections
Long-term construction projects require careful consideration of potential cost increases. Factor in:
- Expected fuel price changes
- Inflation impact on parts and maintenance
- Wage increases for operators
- Environmental regulation changes
- Technology upgrade requirements
Accurate heavy equipment cost calculation requires thorough analysis and regular updates as project conditions change. By considering all these factors, construction managers can better control expenses and maintain project profitability while ensuring equipment availability when needed.
People also read this: 6 Easy Ways to Enhance User Experience on Your E-Commerce Site