✕
In 2022, Indiana University Health began constructing a new hospital, which will be based in downtown Indianapolis.
A consolidation of the city’s Methodist Hospital and University Hospital, the new hospital — a $4.3 billion construction project — has been designed by Indianapolis-based CURIS Design (a collaboration of BSA LifeStructures, CSO Architects and RATIO Design), while St. Louis, Missouri’s HOK is serving as its executive architect.
Aside from CURIS Design’s and HOK’s initiatives, the project will also be overseen by Indianapolis’s Wilhelm Construction and Providence, Rhode Island-based Gilbane Building Company (who will be serving as construction managers), according to Inside Indiana Business.
In addition, Poynter, a sheet metal and custom metal crafter based in Greenwood, Indiana, will be providing sheet metal services throughout the entire project, which is set to be finalized in 2027.
Upon completion, the entire hospital will be more than 2.5 million square feet in size, while providing 864 private inpatient rooms, 50 operating rooms and 110 care spaces within its emergency department. Featuring three patient towers, which will be up to 16 stories high (the first eight floors will be a podium), the entire campus will span 22 acres in all.
“The sheer size of the main hospital, along with its support buildings, the Central Utility Building and the parking garages, sets it apart from Poynter’s other hospital projects,” stressed Zach Piercy, vice president of sales at Poynter Sheet Metal. “A project with this physical size required significant preplanning and coordination.”
Therefore, Poynter approached the project with an entirely different mindset than it typically has for its traditional hospital projects, an approach more in line with a mega project. In particular, it created an overall site management staff, while also dividing the project up into several smaller projects. By doing so, Poynter enabled foremen’s growth and development — with oversight from an experienced leadership team.
“As a result, each leader and install team on the smaller projects could succeed without becoming overwhelmed with the overall project,” Piercy added.
Dividing a Large Project into Manageable Pieces
With regard to dividing such a large project into numerous smaller projects, Poynter didn’t have a team of professionals that only managed the installation of the hospital’s 2,000-plus dampers. Instead, Poynter’s professionals were broken up into area teams, allowing each team’s foreman to focus on their specific areas of the building.
Poynter installed a wide range of volume control dampers too, from small round single blade volume dampers, to 12-foot x 5.5-foot multi-blade, thermally broken exterior air dampers. Life safety dampers of all styles and shapes were installed as well, from 8-inch fire dampers to multi-section dampers that are up to 9 feet wide.
“With our focus on breaking the project down, each release can be broken down to the building, floor, area and even riser — manageable pieces — rather than looking at the overall 2,000-plus purchased dampers,” Piercy said.
When it comes to separating surgery rooms and biosecure areas from less secure areas like cafeterias and lobbies, Poynter strived to simplify foremen’s workloads on these floors, too.
“Our team was able to break apart these areas, giving the more secure areas to our healthcare-focused team members, while letting new team members focus on the less secure areas,” Piercy added.
As an example, the main hospital will have 37 separate air handlers, and every system has a dedicated purpose, from traditional air handlers and energy recovery to N+1 redundancy systems and isolation systems. By finding team members with experience in these specific systems and allowing them to focus on those systems, rather than the entirety of the project, Poynter has protected the overall quality of its work, while also training new foremen.
“Meanwhile, operating rooms will be served by critical environment air handling units,” emphasized Joseph Lansdell, president of Poynter. “Each room is controlled by fast acting air valves on both the return and supply side, allowing the critical spaces to maintain a positive pressure to the surrounding spaces.”
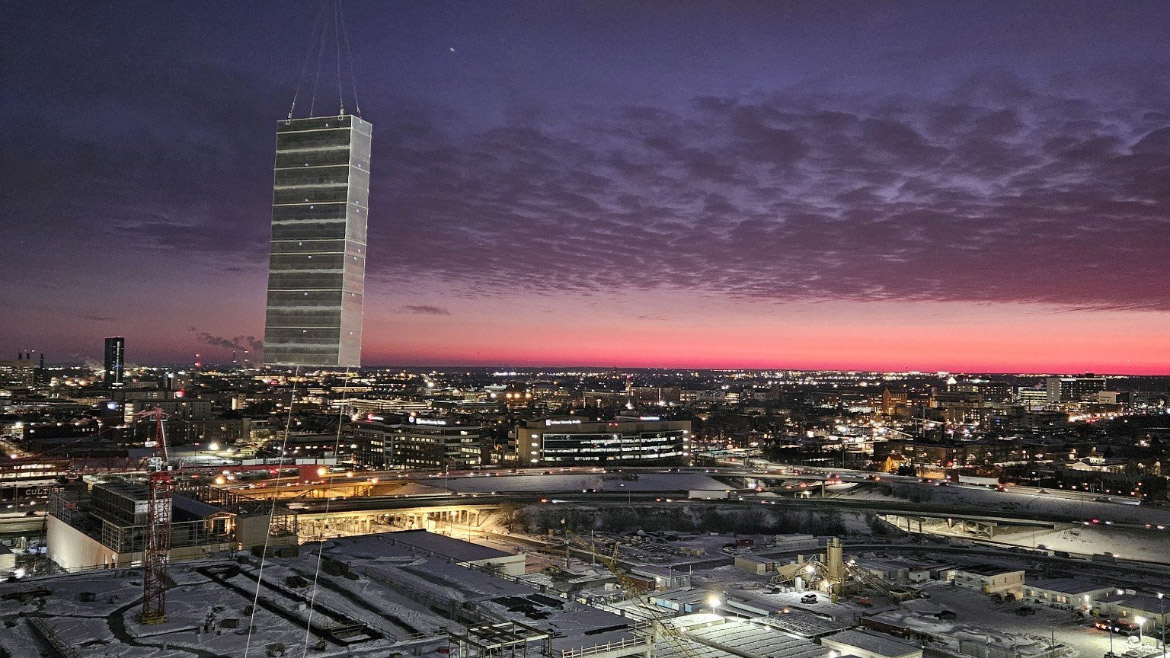
DUCT: Poynter Sheet Metal simplified workloads by breaking the project out into smaller projects. (Courtesy of Poynter Sheet Metal)
The Poynter Standard
While installing new ductwork for the hospital, Lansdell and his team have been focused on maintaining the Poynter standard.
A traditional plan and spec project, the hospital construction process has been associated with air quality, duct sizing and pressure classifications that were developed prior to Poynter’s involvement.
“With that being said, we do play a key role in providing a clean system by protecting all ends at all times,” Lansdell said. “This is a Poynter standard.”
Nonetheless, while planning for the overall project, utilizing large duct sizes and preparing for any potential for pre-fabrication, Poynter has been especially focused on “using the correct product for protection for each circumstance,” according to Lansdell.
“We have been very focused on the risers recently,” he added. “Before starting, we reached out to our peer partner, McGusker-Gill, to learn from their experience with vertical construction.”
Consequently, Poynter has acquired valuable knowledge, concerning the usage of tower cranes to set risers. Additionally, it has obtained new products for duct coverings, which have been especially critical for the larger ducts it’s installed.
“We have really put a focus on limiting the number of open ends by prefabricating sections within our shop, which reduces the amount of potential exposure to the environment while on site,” Lansdell said.
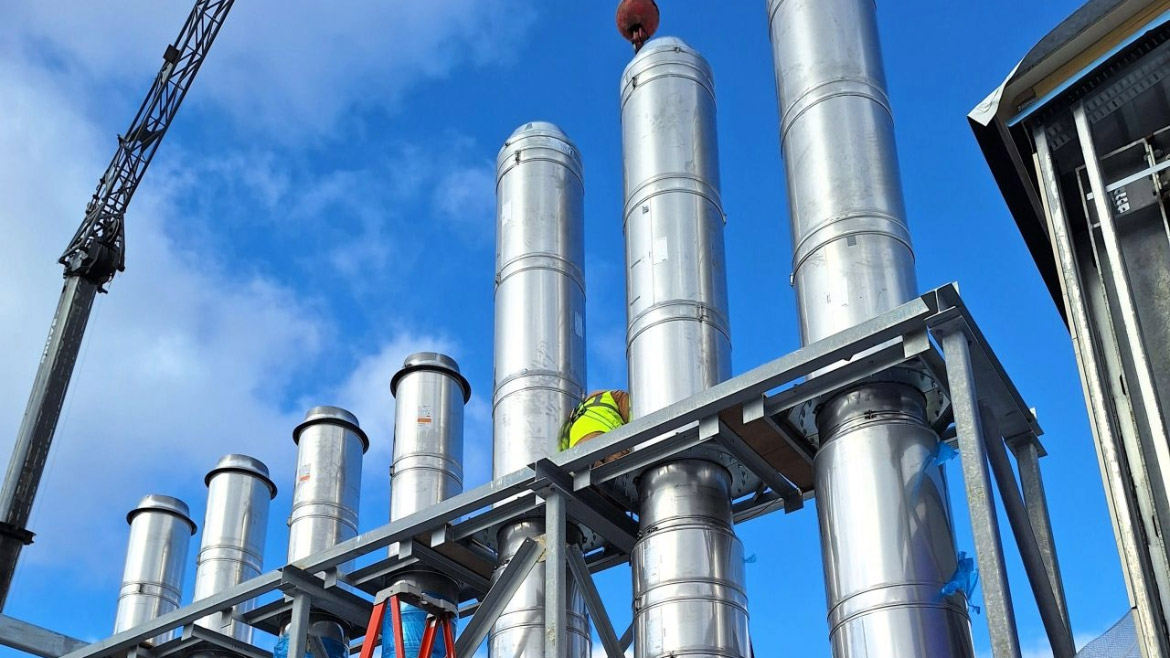
FLUES: Poynter Sheet Metal is implementing a unique approach while managing its latest project, including with boiler flue installation at the central utility building. (Courtesy of Poynter Sheet Metal)
Installing Boiler Flues, Minimizing Fire Issues
In addition to installing dampers, air handling units and ducts, Poynter was hired to install a variety of boiler flues for the hospital’s Central Utility Building.
Different types of boiler flues are being used for different types of systems, as Poynter has installed eight 20-inch, double wall stainless steel generator flues that have 4 inches of ceramic insulation. Moreover, it’s installed four 20-inch AL29-4C SS boiler flues, along with three 24-inch double wall stainless steel steam boiler flues.
As these boiler flues were installed, CURIS Design’s engineering team had to consider a crucial issue: hospitals’ typically high air change out rates, when compared to other public spaces’ rates. After all, in the instance of severe cases like wildfires, filters often have to be changed daily.
In preparation for such issues, CURIS Design’s engineering team “did an exceptional job at breaking areas down by classification to allow for all potential hazards to have alternative methods,” according to Piercy.
This is especially obvious with regard to the systems that are serving the hospital’s three patient towers, as every room is being served and controlled by terminal units — with supply, return and exhaust. Thus, there is high adaptability as containment and isolation zones are created within the systems.
“CURIS Design’s engineering team did a fantastic job while looking at the facility’s long-term functionality,” Piercy said.
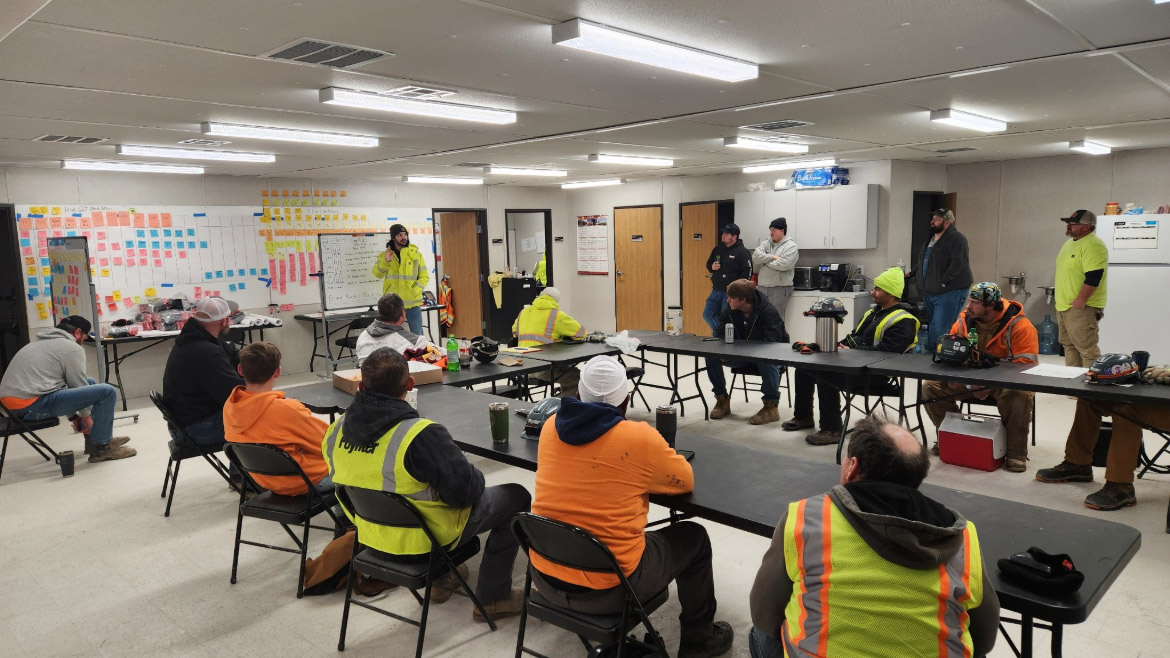
MENTOR: Poynter’s mentorship opportunities have been increasing at a rapid pace. (Courtesy of Poynter Sheet Metal)
Preparing for the Future
While reflecting on the last two years, Piercy believes Poynter’s entire approach to the hospital construction project has had the future in mind.
“When you look at the total duration of this project, there is a potential for a new apprentice to serve their entire apprenticeship at one jobsite,” he stated. “On the same hand, with so many employees on site, there is an opportunity to let upcoming employees manage a smaller project within a larger project, while having built-in mentorships on the same site.”
Hence, Poynter will be able to fully maximize a transfer of experiences and knowledge from its foremen to its next generation of leaders. Due to the Indiana University Health hospital project alone, Poynter’s mentorship opportunities have been increasing at a rapid pace.
“Simple aspects, such as scheduling work and coordination with shared resources like loading docks and cranes, has allowed newer leaders to perform the process, but also see how their peers plan,” Piercy said. “All of the leaders on site have been working together to ensure the project’s overall success, from scheduling deliveries to internal safety audits.”
And, in turn, Indiana University Health will not only have a highly safe hospital for its patients, but Poynter’s next generation of leaders will be fully prepared to help create other safe facilities throughout the United States during the second half of the 2020s — and beyond.