✕
As the HVACR industry continues to adapt to evolving environmental regulations, refrigerant management has emerged as a critical focal point. This is particularly true in light of the Environmental Protection Agency’s (EPA’s) Emissions Reduction and Recycling (ER&R) program, a recent initiative aimed at improving the management, recycling, and reuse of HFCs under the AIM Act.
At this year’s AHR Expo, companies showcased strategies and solutions aimed at helping contractors and end users comply with EPA’s new refrigerant management regulations.
Managing Refrigerants
Compliance with any regulation is key to its ultimate success or failure, and the ER&R program is no exception, said Adam Dykstra CFO of FMHero. He noted that the three key provisions in the program include:
- Reduction in the leak rate threshold on nearly all systems with 15 lbs. or more of refrigerant, starting in 2026;
- Required use of reclaimed refrigerant in supermarket systems, refrigerated transport, and automatic commercial ice makers, starting in 2029; and
- Newly clarified and specified handling of disposable cylinders and their heels, starting in 2028.
“Time will tell if market-based incentives and EPA’s stated enforcement and compliance initiatives targeting Section 608 and the AIM Act will impact the individual technician and contractor significantly enough to gain compliance in the industry and result in a successful ER&R program,” said Dykstra. He added that a solid refrigerant management solution is the only sure-fire way to remain compliant.
Refrigerant management is critical for several reasons, said Michael Pennington, director of engineering at Heatcraft Refrigeration Products.
“The primary benefits include ensuring the availability of higher-GWP refrigerants to allow continuing operation of equipment until the end of its useful life, as outlined in EPA’s Technology Transition rule, while minimizing propagation of these higher-GWP refrigerants over time.”
At the AHR Expo, Heatcraft showcased its comprehensive low-GWP product line, which included sensing and mitigation solutions that are fully compliant with regulations. Supported by advanced equipment selection tools and configurations, Heatcraft commercial refrigeration equipment is thoughtfully engineered with customers in mind, said Pennington.
“We have developed useful tools that make navigating new regulation requirements clear and simple, offer maximum flexibility, and enable cost control in all application scenarios.”
PREVENTING COUNTERFEITS: Strong refrigerant management can help prevent illegal and counterfeit refrigerants from entering the market. (Staff photo)
Minjin Kim, global marketing manager at The Chemours Company FC LLC, pointed out that refrigerant management is crucial to ensuring the industry maintains an adequate and legal supply of HFCs to service existing equipment. Strong refrigerant management can also help prevent illegal and counterfeit HFCs from entering the market. This is important, said Kim, as illegal/counterfeit refrigerants can compromise system performance, damage equipment, and possibly put technicians and end users at risk.
Refrigerant recovery is also a key part of properly managing refrigerants, said Kim.
“Recovery will become increasingly important for servicing and retrofitting existing equipment as HFC phasedowns continue and technology transition ‘sector controls’ are put into place.”
Leak detection and repair are essential components of effective refrigerant management as well.
“Detecting, then fixing, leaks as early as possible will support efforts to ensure adequate HFC supply exists,” said Kim. “It will also move the industry forward in reducing HFCs’ contribution to global warming. Better leak detection systems can also translate into better equipment cooling performance, improved energy efficiency, and ultimately lower maintenance costs.”
Establishing strong refrigerant management practices can help ensure that refrigerants are properly handled, recovered, recycled, and disposed of, while helping businesses to remain competitive and meet consumer demands, said Dr. Chris Seeton, applications director of Orbia Fluor and Energy Materials (Koura).
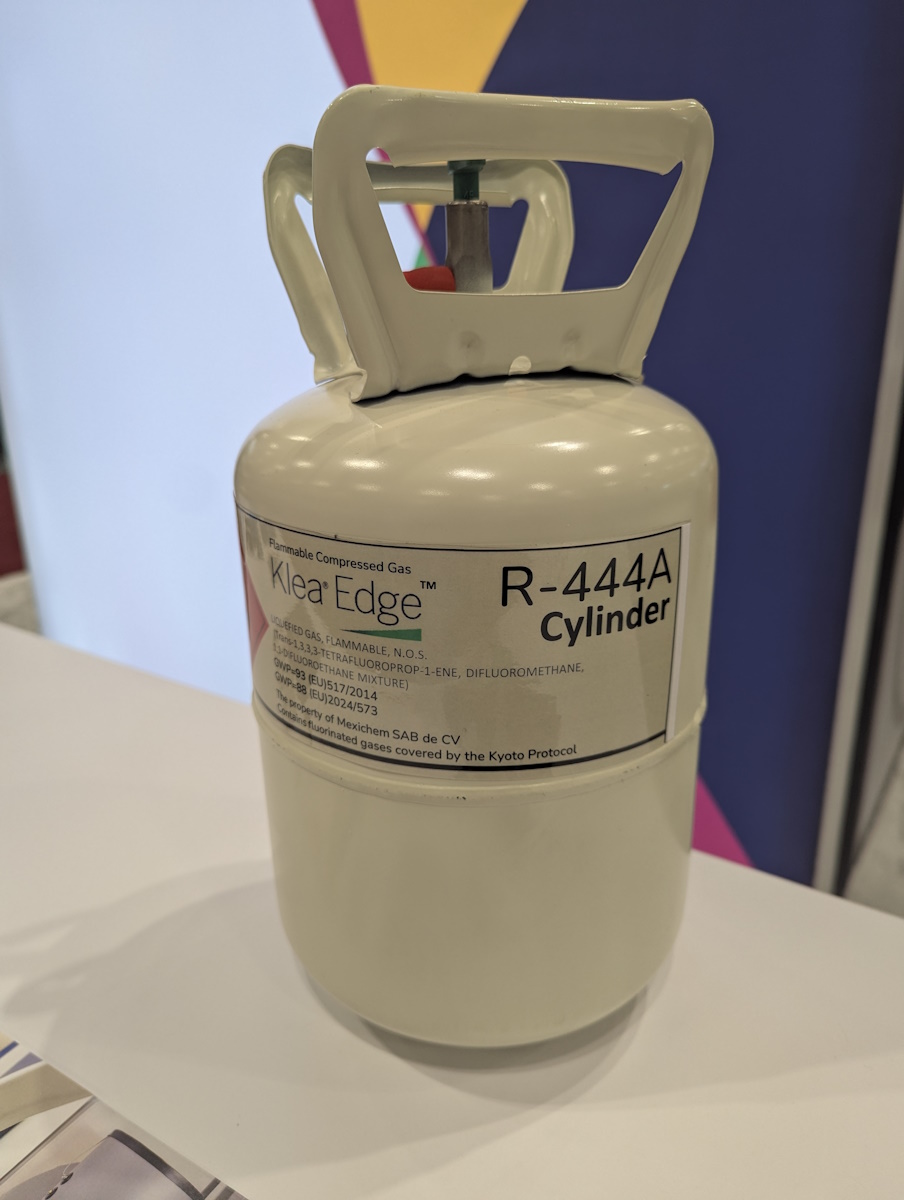
LOW-GWP SOLUTION: Klea Edge R-444A is a low-GWP solution suitable for appliance applications that currently use R-134a or R-1234yf. (Staff photo)
“Refrigerant management programs can also extend the service life of the equipment to avoid forced early retirement of the systems, due to the transition of the refrigerants to lower-GWP limitations,” said Seeton. “Going forward, servicing existing equipment will be concentrated around the availability of refrigerants used in the marketplace. Most of the existing equipment is designed for non-flammable products, while the new equipment is focused on the A2L HFO-based products. This transition time will be decades in the making, as the lifetime of commercial equipment is long, and the refrigerants must be managed as replacements are introduced and adopted.”
At the AHR Expo, Koura highlighted several of its low-GWP refrigerants, including Klea 473A, an ultra-low temperature refrigerant that replaces R-23 and R-508B in high-value cold chain, medical, and pharmaceutical applications. Also featured were Klea 456A and Klea Edge 444A, which are low-GWP solutions suitable for appliance applications that currently use R-134a or R-1234yf, while Klea Edge 485A is a high-performing, enhanced CO2 refrigerant for heat pump and air conditioning systems designed for R-744 (CO2).
Safety is another reason why refrigerant management is so important for commercial refrigeration applications, said David Reitz, U.S. strategic partnerships and business development at Matelex.
“With high leakage rates, high energy consumption, and no supervision, food safety — and that of all products subject to refrigeration — becomes Russian roulette,” said Reitz. “Fluid levels need to be monitored at all times, and alerts triggered in the event of an anomaly, so that rapid action can be taken to avoid production stoppages or breaks in the cold chain. Remember that with direct detection alone, safety is not guaranteed — 24/7 monitoring is necessary, not just in one place.”
Reitz added that leaky installations also consume much more energy and require recharging with expensive refrigerant.
“All these factors have a major impact on company finances, which is why informed fluid management is necessary to limit the financial impact of cold production.”
To that end, Matelex highlighted several of its solutions that are designed to optimize refrigeration system management. PolarBox uses the Internet of Things (IoT) to collect and analyze data from installations, helping to prevent issues like refrigerant leaks. The data can be accessed through the PolarVisor interface for real-time monitoring, performance analysis, and malfunction alerts. Additionally, the Energy Module tracks energy consumption, providing a comprehensive overview of system efficiency to help lower operating costs.
Make a Plan
As regulations around refrigerant use tighten, more commercial end users will look to their contractors for assistance in creating a comprehensive refrigerant management plan. According to Seeton, a refrigerant management plan should include best practices, including inventory checks of all systems and their refrigerant and charge levels; leak detection and repair; proper disposal of old or unused refrigerants; monitoring technology; appropriate training of staff (ensuring certifications); and environmental compliance including recording of all refrigerant leaks, repairs, storage, and disposal activities.
“Contractors need to understand the proper management of the refrigerants put into the systems and collect and recycle from the systems, serve the purposes of not only the moral obligation to prevent the leakage but also the legal compliance,” said Seeton. “They need to take the ownership of the refrigerant of the systems that they service, to ensure the accountability of the refrigerants being properly collected, recycled, or sent for reclaim or destruction, and prevent any leakage as much as possible. More refrigerants leakage today means less refrigerant availability in the future to service the refrigeration equipment.”
End users aren’t the only ones who need a well-documented refrigerant management plan — contractors and technicians do, too, said Dykstra. He added that the key to any successful refrigerant management program is detailed zero sum documentation.
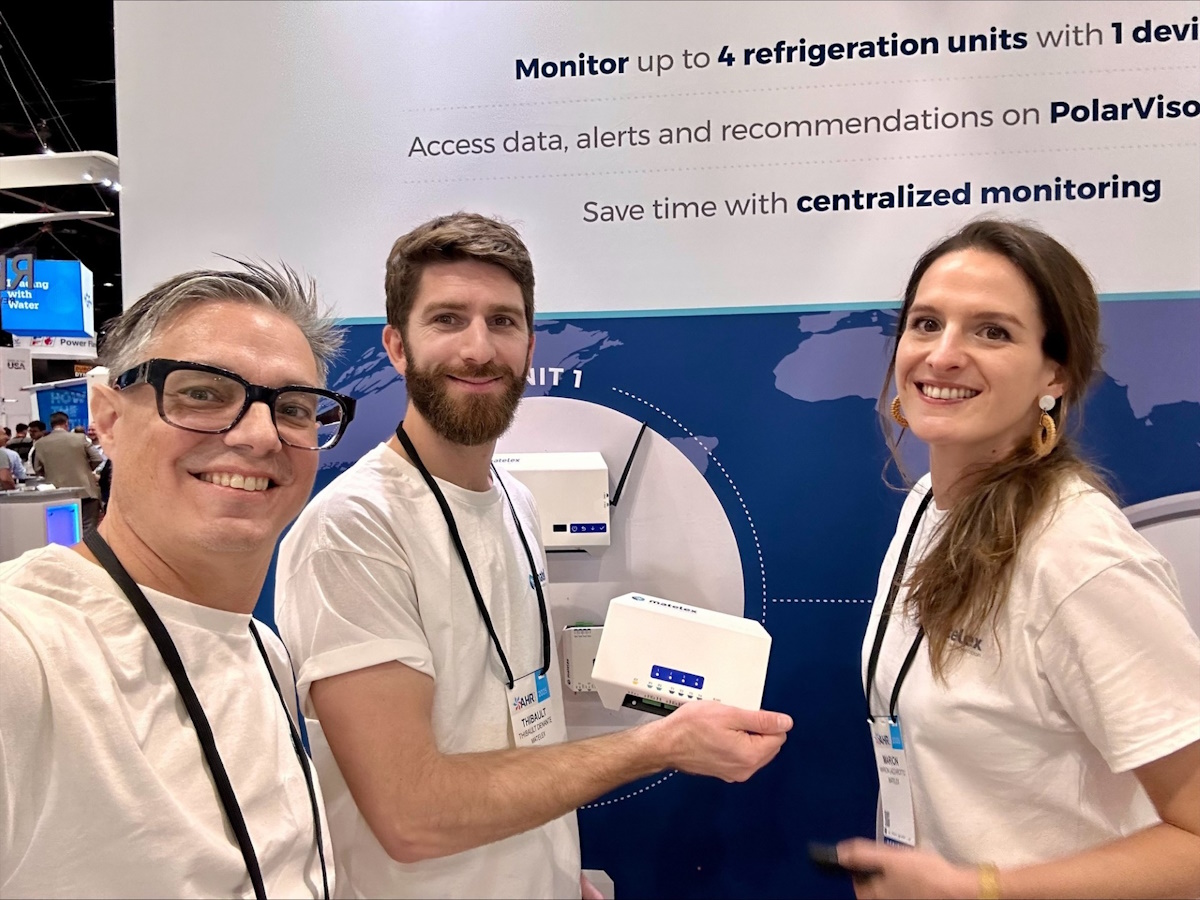
REFRIGERATION MANAGEMENT: From left to right, Matelex’s David Reitz, Thibault Denante, and Marion Lazzarotto show off the PolarBox refrigeration management system. (Courtesy of Matelex)
“For contractors, this means tracking every ounce from purchase, through inventory, charge events, disposable/refillable cylinder handling, recovery, and documented delivery to a reclaimer or wholesaler,” he said. “For equipment owners or operators, this means tracking and documenting every system, charge, recovery, repair, leak inspection/reinspection, and all refrigerant inventory. With those key elements, the inevitable outcome is a lower cost of operation, liability reduction, and regulatory compliance.”
To assist with that compliance, FMHero showcased its refrigerant management platform, Single Source of Truth, at the AHR Expo. According to Dykstra, this end-to-end solution for refrigerant management and compliance is tailored for technicians, contractors, and equipment owners.
“FMHero simplifies compliance and eliminates typical data entry errors at every level of the refrigerant management process for all stakeholders,” he said.
Kim emphasized that a refrigerant management plan helps businesses at every level of the HVACR industry create a solid strategy based on the “Eight Rs.” These include keeping up to date on regulatory changes, while recordkeeping ensures audit readiness and boosts operational efficiency. Repairing leaks reduces refrigerant costs and improves system efficiency, and replacing old systems with higher-efficiency A2L units reduces energy consumption. Retrofits can convert equipment to more sustainable refrigerants. Recovery ensures refrigerant is removed from a system and safely stored, while reuse/recycle returns it to the same or another system with common ownership. Finally, reclamation reprocesses recovered refrigerant to virgin standards, ensuring a reliable supply for servicing.
“By following these eight guidelines, contractors can align their businesses with regulations and ensure they have the resources necessary to continue servicing equipment with legacy refrigerants, as well as to successfully introduce A2L solutions to customers,” said Kim.
If contractors or end users need more information about implementing strong refrigerant management practices, refrigerant manufacturers like Chemours, as well as OEMs, can be excellent resources, said Kim. “Our strong understanding of the supply chain of HFCs and new-generation HFOs can help contractors and assist equipment owners in finding retrofit refrigerant options and making repair/replace decisions. We can also help gauge to what extent — and how urgently — they need to recover, reuse, and/or reclaim refrigerants during system service and end of life.”